CNC Machines
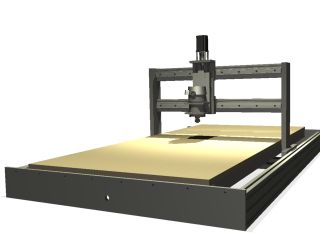
In order to understand where CNC Machining first appeared, it is important to note that the said machine’s advent can be traced back to the invention of the NC (numerical controlled) machine made by John T. Parsons during the 1940s-1950s. The NC was a breakthrough invention that led the way towards modern automated machines.
CNC mills have very little differences with its predecessor in terms of its concept. The modern CNC mill still functions in machines to produce outputs in three dimensional directions: X and Y axes, and depth. Examples of CNC systems applied in various industries include laser cutting, welding and ultrasonic welding among others.
CNC Motors
CNC motors are the heart of any CNC machine. The size and type of motor can define a CNC routers precision, speed, and accuracy. There are two primary classes of motors used on CNC machines, stepper motors and servo motors. Within these two classes there are several types.
Stepper motors
CNC motors are the heart of any CNC machine. The size and type of motor can define a CNC routers precision, speed, and accuracy. There are two primary classes of motors used on CNC machines, stepper motors and servo motors. Within these two classes there are several types.
Stepper motors
mid-sized CNC mills & milling machines, CNC lathes, Pick-n-place machines, Laser Engravers and Laser Cutters, Vinyl Sign Cutters, CNC Plasma Cutters, and CNC Foam Cutters. These motors have been used in precision telescope positioning systems and robots.
Block Diagram of CNC Machine

MACH3 CNC Controller
Mach3 turns a typical computer into a CNC machine controller. It is very rich in features and provides a great value to those needing a CNC control package. Mach3 works on most Windows PC’s to control the motion of motors (stepper & servo) by processing G-Code. While comprising many advanced features, it is the most intuitive CNC control software available. Mach3 is customizable and has been used for many applications with numerous types of hardware.
Here are some of the basic features and functions provided by Mach3:
- Converts a standard PC to a fully featured, 6-axis CNC controller
- Allows direct import of DXF, BMP, JPG, and HPGL files through LazyCam
- Visual Gcode display
- Generates Gcode via LazyCam or Wizards
- Fully customizable interface
- Customizable M-Codes and Macros using VBscript

G-Code and M-Code list of CNC Machines
DIY Small CNC
Designing A CNC machine from scratch is a good idea and a enjoyable hobby but a Time consuming and patient job.
What type of machine you are going to design its depend your application, job size and of-course your pocket weight and volume.
But it is always desirable to start with a small one and you can built a bigger one once you get idea and familiar with all the equipment and controller .If you are agree let's start to design the machine.
What you need
3/4" thick wood planks, 1/4 threaded screw,some brass bushes, 3 nos of stepper motors,
one old PC (equipped with OLD LPT1 printer port)Loaded MACH3 software,Stepper motors driver board, High speed DC motor for spindle drive and power supplies.